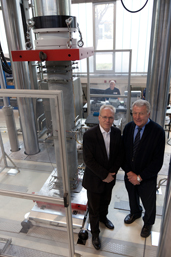
Große Freude im Otto-Mohr-Laboratorium (OML) der Fakultät Bauingenieurwesen: Eine neue Prüfmaschine ist nach 18 Monaten Bauzeit offiziell in Betrieb genommen worden – und es ist eine große, die ihresgleichen in Deutschland sucht. „Mit dieser 10-MN-Säulenprüfmaschine steht der TU Dresden eine Versuchseinrichtung für großformatige Bauteile zur Verfügung, die den internationalen Vergleich nicht zu scheuen braucht!“ schwärmte der Direktor des Otto-Mohr-Laboratoriums, Prof. Manfred Curbach, bei seiner kurzen Rede zur Einweihung der Maschine.
Erste Überlegungen für die Anschaffung gab es seit 2004, aber erst im April 2009 konnte das Bauvorhaben begonnen werden. Die Prüfmaschine wurde unter laufendem Betrieb installiert, was nicht immer ein Zuckerschlecken für die Mitarbeiterinnen und Mitarbeiter sowie die Forscherinnen und Forscher im OML war: „Wenn man heute hier steht, sieht man nicht, dass für die Sicherung der Baugrube 182 Ortbetonpfähle mit einer Länge von jeweils knapp 10 m erforderlich waren, um den schlechten Baugrund zu überlisten, damit eine Baugrube mit vier Metern Tiefe, dreieinhalb Metern Breite und 18 m Länge entstehen konnte. Diese Baugrube musste anschließend mit einer Betonwanne verstärkt werden, um einen Grundwassereinbruch zu verhindern. Man atmet nicht den Staub ein, hört nicht den Lärm oder spürt die Erschütterungen, die wochenlang die Arbeiten in der Versuchshalle beeinträchtigten“ resümierte Dr.-Ing. Torsten Hampel, der Leiter der Versuchshalle. Aber der Zusammenhalt aller Beteiligten habe zu einem reibungslosen Gelingen beigetragen – wobei er ausdrücklich alle Beteiligten einschloss: „Alle haben an einem Strang gezogen und diese komplizierte Maschine umgesetzt: die TU Dresden, das Sächsische Immobilien- und Baumanagement (SIB), die Planer, Bauausführenden, Maschinenbauer und die Mitarbeiter des Labors und des Instituts.“
Spannende Momente gab es reichlich beim Aufbau der Prüfmaschine. Das fing an bei sprachlichen Verwirrungen – die Maschinenbauer kamen von der Firma walter+bai aus der Schweiz und sprachen für hiesige Ohren unverständliches Schwytzerdütsch. Und die hiesigen Mit-Aufbauer sind des für normale Schweizer durchaus unverständlichen Sächsisch mächtig. In kniffeligen Situationen konnte man sich allerdings auf eine Art Hochdeutsch einigen und doch ganz gut verständigen. Und immer wieder machte die Größe der Maschine es nicht leicht: Für die Montage war beispielsweise ein Autokran erforderlich, der 200 Tonnen heben konnte. Aber er passte nur gerade so in die Versuchshalle hinein: Dieser Autokran war alleine 15,50 m lang, es standen aber nur 16,50 m Rangierlänge zur Verfügung. Es dauerte eineinhalb Stunden, bis das Fahrzeug an dem Platz stand, von dem aus gerade so das schwerste Maschinenteil an der Fensterfront entlang in die Grube versenkt werden konnte!
Aber das alles ist nun Geschichte – die 10-MN-Säulenprüfmaschine steht. Sie ist so ausgelegt, dass sie den unterschiedlichsten wissenschaftlichen Aufgabenstellungen gerecht wird. In dieser Versuchseinrichtung können Balken mit einer Stützweite von bis zu 15 Metern und einem Eigengewicht von bis zu 120 Tonnen untersucht werden, was zum Beispiel den realen Abmaßen von Brückenteilen entspricht. Gleichzeitig steht mit vier Metern Höhe auch in der Vertikalen ausreichender Raum für große Versuchskörper oder die zusätzliche Anordnung von schon vorhandenen Belastungseinrichtungen zur Verfügung. „Somit entstand eine universell einsetzbare Prüfeinrichtung, deren Prüfkapazität schon jetzt für das kommende Jahr komplett ausgebucht ist“, freut sich Prof. Manfred Curbach.
Den ersten Versuch führten Mitarbeiter des Otto-Mohr-Labors noch während der kleinen Feierstunde durch, bei der sich viele der am Bau der Maschine Beteiligten wieder sahen: Eine zwei Meter hohe Stütze, die mit Carbon verstärkt war, wurde langsam aber stetig immer größerem Druck ausgesetzt. Am Ende machte es allerdings nicht „Knall“ oder „Peng“, sondern lediglich „knrrrsch“ – ein durchaus erwünschter Effekt, denn im wahren Leben sollen die Stützen ja große Belastungen aushalten und durch zuvor einsetzende Rissbildung ihr Versagen ankündigen…